【実践事例②】納期遅延・現場疲弊・利益不透明の三重苦から脱却
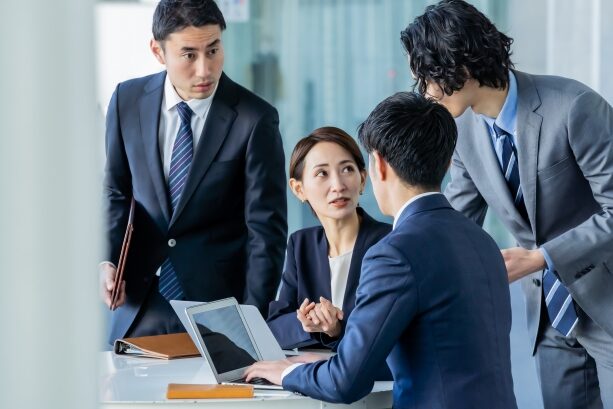
―― 精密機器メーカーが半年で利益率11.8%を達成するまでの軌跡
◆ はじめに
今回ご紹介するのは、愛知県に本社を置く従業員数2000名の精密機器メーカー様です。長年にわたり高精度な部品加工で顧客からの信頼を集めていたものの、近年は納期遅延や利益低迷に悩まされる状況が続いていました。
現場は疲弊し、経営層は「どこに手を打てばよいのか分からない」と混迷の最中。そんな中、F6 Designが伴走支援させていただくことになりました。
◆ クライアントが抱えていた3つの根深い課題
ヒアリングと現場観察を通して浮かび上がったのは、以下のような3つの構造的課題でした。
① 納期遅延が常態化し、顧客クレームが多発
受注から納品までのリードタイムが予定通りに進まず、納期に間に合わないケースが頻発していました。とくに量産ラインでの変更指示や段取り替えが多く、全体工程が日々揺れ動いている状態。
その結果、営業担当が顧客対応に追われ、社内外の信頼関係にひずみが生じていました。
② 現場が疲弊。都度変更の生産指示に対応しきれない
工程担当者からは「また段取りが変わった」「この前と指示が違う」といった声があふれ、指示待ち・確認作業に追われる“非生産時間”が日常化。属人的な調整でなんとか乗り切っている状況で、組織としての再現性に欠けていました。
③ 原価構造がブラックボックス化、利益が読めない
会計システムにはデータがあるものの、製品ごとの原価・利益が見えない状態。
「なんとなく粗利が出ていそう」「工場は忙しいから儲かっているはず」といった勘と経験による経営判断に頼らざるを得ない状態でした。
◆ F6 Designのアプローチと実行施策
私たちがまず行ったのは、「原因を表層ではなく構造で捉えること」です。
以下の3つの軸で、徹底的に可視化と仕組み化を図りました。
1|生産スケジュールの見える化支援(アナログ×デジタル)
- 各ラインの作業計画を日単位で表示するホワイトボードを導入
- 現場で毎朝の朝礼時に稼働予定を共有・チェック
- さらに、Googleスプレッドシートによる進捗可視化表を作成し、管理者間の共通言語を定着
これにより、変更があっても関係者間で即座に共有され、手戻りが圧倒的に減少しました。
2|業務プロセスの標準化(3工程→2工程へ統合)
- 現場ごとに異なっていた組立手順を整理し、ライン設計そのものを見直し
- 「加工→検査→出荷」だった3工程を「加工・検査→出荷」の2工程へ再編
- 工程の切り替え回数を減らすことで、無駄な待機時間や移動ロスを削減
同時に、マニュアルの刷新と教育制度の導入により、新人でも同じクオリティの作業が可能になりました。
3|原価構造の項目別整理と、損益シミュレーション表の導入
- 原価項目を「材料費・外注費・人件費・間接費」に分類し、各製品別に配分ルールを設計
- Excelベースのシミュレーションシートを作成し、「この製品を月100個つくったら粗利は○円」と経営判断に使えるIT補助ツールを構築
- 部門リーダーともこの表を共有し、現場と経営が同じ“数字”を使って会話できる環境を整備
◆ 結果として得られた3つの変化
施策を着実に運用しはじめてから、わずか3ヶ月で成果が目に見える形に。半年経過時点では、社内に大きな変化が定着していました。
✅ 納期遵守率:68% → 94%
朝礼による日次確認と、スケジュールの事前共有により、突発的な混乱が大幅減少。営業からの感謝の声も多数寄せられました。
✅ 工程の作業時間:27%削減
ライン再設計により、スタッフの手持ち時間が減少し、工程にリズムが生まれるように。
✅ 利益率:6.3% → 11.8%(半年後)
製品ごとの価格戦略や、受注判断にも“利益”の視点が組み込まれ、収益体質が根本から改善されました。
◆ クライアントからの声
「“改革”という言葉に身構えていたが、F6 Designさんは現場の声を一番聞いてくれた。現場と経営、両方の目線があるから信頼できた。」
「数字で会話できるようになったことで、会議の質も一気に上がった。今では月次報告が楽しみです。」
◆ まとめ
この事例は、どの業界でも直面しうる「納期・効率・利益のジレンマ」を、属人化ではなく“仕組み”で打破した典型的な成功例です。そしてこの部門の成功例はクライアント内で全社展開され標準化されました。つまりはひとつの現場からの成功例が会社全体まで浸透したということです。”数値結果”は会社を変革できることを体現できた事例となりました。
F6 Designは、正論を語るだけのコンサルではありません。
現場で一緒に汗をかきながら、課題を分解し、改善策を組み立て、成果が出るまで伴走します。
同じような課題を感じている企業様、ぜひ一度お気軽にご相談ください。